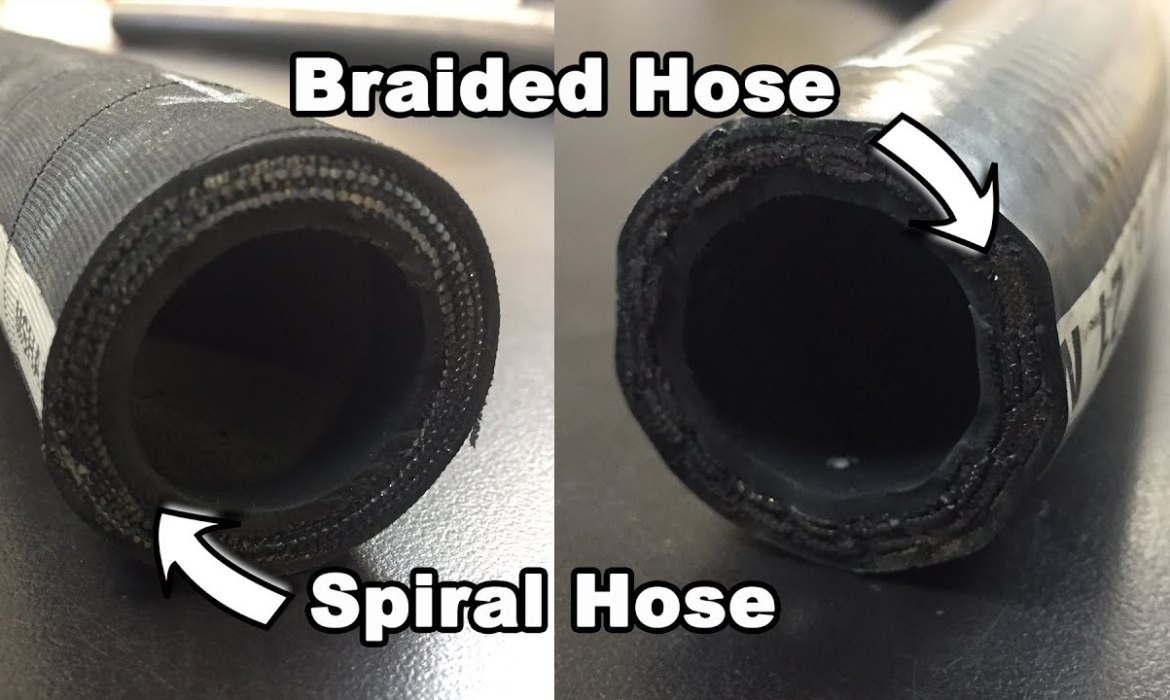
Hydraulic terminology identifies hoses as vital components in hydraulic systems and is used as flexible media to transfer high-pressure hydraulic fluid. During the design of such hoses, their performance, expected life, and applications are specified. Spiral and braided hoses are some of the most common hydraulic hoses; however, each has varying characteristics that make them useful for other applications. Knowing these differences is crucial in getting the right hose for your needs. Today in this post, let’s understand some critical differences between spiral and braided hydraulic hoses.
Construction Differences
The prime difference between spiral and braided hydraulic hoses is in their fabrication. Braided hydraulic hoses typically have one or two support layers consisting of a steel wire braided internal tube. This kind of braided fabrication gives the hose flexibility without compromising the quality.
Spiral hydraulic hoses, on the other hand, have four or six layers of fortification with the steel wires wound in a spiral fashion. This construction gives a more tough hose that can hold higher weight levels. When selecting the hydraulic hose, one can refer to a renowned production line to know which fabrication fashion is best for the application.
Flexibility and Bend Radius
Another essential feature that differentiates spiral hydraulic hoses from braided ones is flexibility. For the latter, these hoses boast excellent flexibility and tight bend radius, thus making them much easier to install and route in complex hydraulic systems. The braided construction can explain the flexibility, which gives the hose a bend radius without kinking, putting stress on the reinforcement layers.
On the contrary, spiral hoses have fewer flexible properties due to their construction from multiple spirally wound layers of wire. This rigid construction gives spiral hoses a larger bend radius. Hence, spiral hoses become more challenging to install in tight spaces. Spiral hoses, however, can be recommended by a hydraulic hose factory for use, for which flexibility is less of an issue and higher pressure is required.
Durability and Wear Resistance
Durability is always a significant basis in hydraulic hose selection, especially in challenging environments. Spiral hydraulic hoses are more resilient and have better wear resistance than braided ones. Additional durability is derived from the spiral construction that allows it to bear up better to abrasion, external damage, or other sources of wear.
Spiral hoses will also not fatigue or fail under repeated cycles of high pressure as rapidly and, therefore, become very reliable choices for heavy-duty applications. In contrast, while resilient and hard-wearing, braided hoses work more in high-pressure situations and are susceptible to wear and tear. If you’re looking for a long-lasting hose, you’ll want to keep reading to find out why spiral hoses work best in the most demanding conditions.
Application Suitability
The suitability of spiral versus braided hydraulic hoses is primarily based on application requirements. One can expect the braided hose variation in most mobile equipment, such as construction or agricultural equipment, that requires flexibility and managing moderate pressures. Due to their ease of bending and medium to high-pressure handling capabilities, they are most appropriate for such applications.
On the other hand, Spiral hoses are more relevant in non-moving machinery and heavy-duty industrial applications where massive resistance to pressure and durability are required. Consultation with a hydraulic hose factory will help determine which hose is most appropriate for your application.
Pressure Handling Capabilities
One of the notable differences between spiral and braided hydraulic hoses is their capability to handle pressure. Braided hoses normally do well under pressure, especially when the formation is flexible, which makes them perfect for applications under medium or high pressure. Spiral hoses, however, are designed for extreme pressure applications since they have multiple layers of spiral-wound steel wire.
Such hoses can sustain much higher pressure levels than their braided counterparts; hence, they are ideally suited for heavy industrial use. If you need a hose that will take very high pressure, you will want to read more about the advantages of spiral hoses.
Cost Considerations
The cost factor is always at the top when selecting any hydraulic hose. In general, braided hoses are less expensive than spiral hoses because they are more straightforward to fabricate and, on top of that, usually have lower pressure ratings. The ease of fabrication related to them translates into braided hoses becoming attractive in many applications where low pressure isn’t a factor.
While spiral hoses are more expensive, the increased pressure resistance and durability might pay for themselves over time, especially when hose failure can result in costly downtime or equipment damage in high-pressure uses. The cost of investment, however, has to be weighed against the potential savings over long periods.
Endnote
One chooses a spiral or braided hydraulic hose based on pressure needs, flexibility, durability, application, and cost. Braided hoses are flexible and good for medium—to high-pressure uses; spiral ones excel in extreme pressure and heavy-duty usages. Consult with a Hydraulic Hose Factory to select the correct hose for your system and ensure optimal performance.
Read More From C-incognito